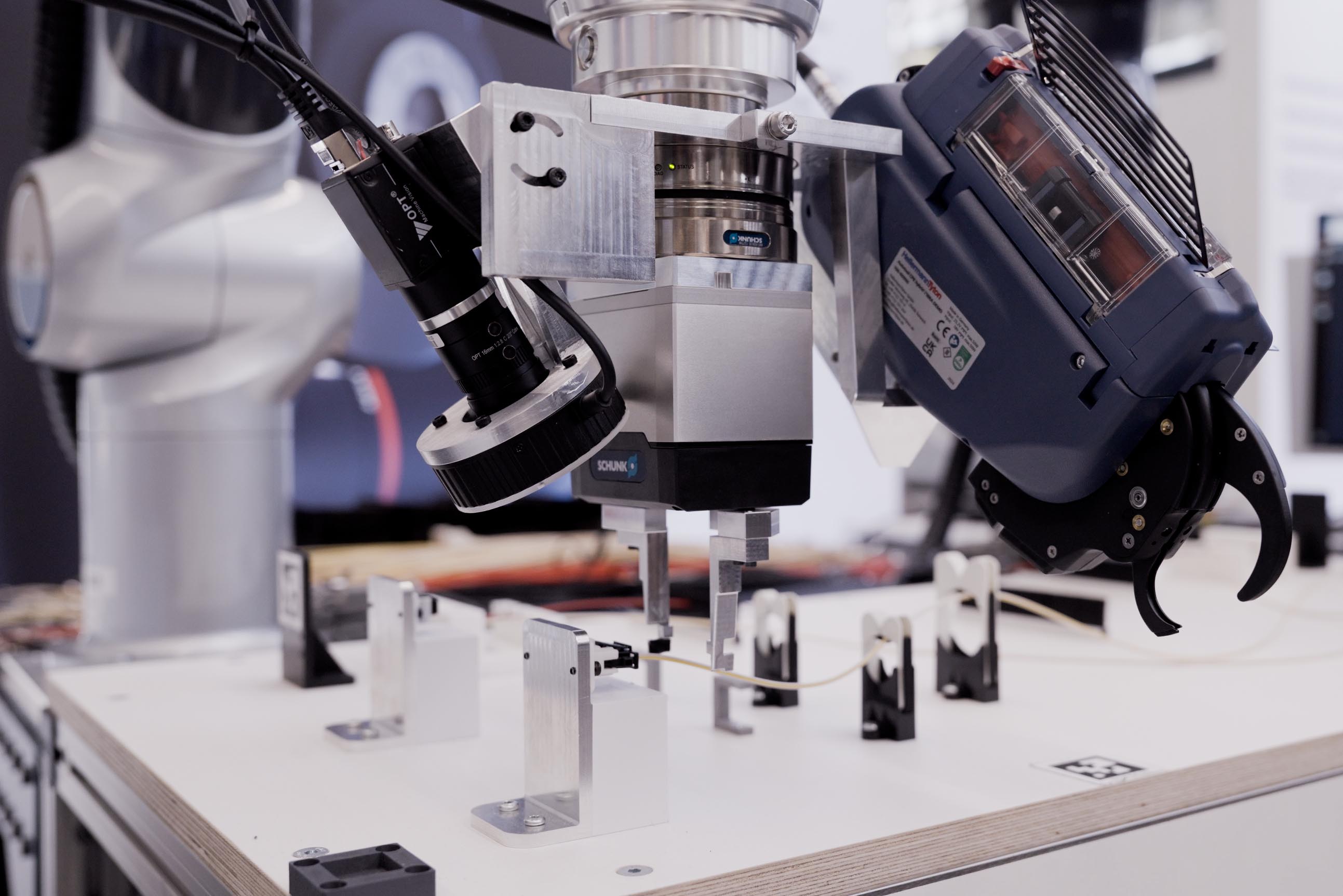
Robotik Challenge 2025: The solution behind the award
/ 5 min readThe publicly funded Transformations-Hub Leitungssatz project has once again welcomed participants to the Robotik Challenge at the ARENA2036 research campus in Stuttgart. This year’s focus is on automating the production of partial wire harnesses - one of the least automated areas in automotive manufacturing. As a member of ARENA2036 and a leader in AI-driven automation solutions, we have developed an innovative solution that meets this challenge with human-like dexterity in only 2:25 minutes - 35 seconds less than the required cycle time. As the fastest team, we were honored with the award for “Economic efficiency”.
The tasks
The wiring harness of a vehicle, also known as the cable harness, can span several kilometers and serves as the car’s nervous system. Comprising wires, connectors, sensors, and protective sheathing, it ensures seamless signal transmission and power distribution across all electrical and electronic components.
The partial wiring harness, which is at the center of the Robotik Challenge, is a sub-unit of the complete wiring harness. The task primarily involves placing five wires into four different connectors, utilizing Nano MQS contacts, low-profile cables, connectors, and cable ties.
Despite significant progress in automation, the production process remains largely manual. The reason lies in its complexity: many robots struggle with the required dexterity, high variability, and necessary precision.
Handling the flexible wires requires great dexterity, as the connectors need to be positioned with precision and the applied force must be carefully controlled. Intelligent technologies, including advanced sensors and AI-assisted camera systems, are essential to mastering these challenges.
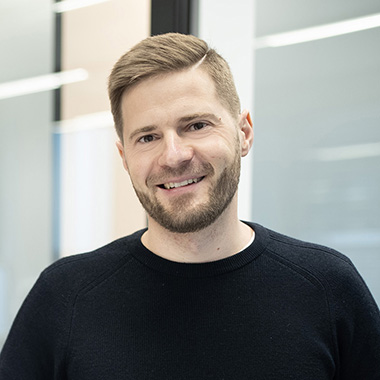
Skilled workers take around two minutes to manually produce the specified partial cable harnesses. Our goal was to closely match this time to highlight the efficiency of robot automation. With a cycle time of just under two and a half minutes, we met this challenge and won the award for Economic efficiency.
Our solution
For fast, efficient, and precise execution of the Robotik Challenge, our team relies on two of our Diana 7 robots. These seven-axis robots are highly flexible, powerful, and incredibly precise. Additionally, we use two 2D camera systems with ring lights, external force-torque sensors, a cable tie tool, and several magnetic closers.
The assembly process is divided into several meticulously timed steps that require a balance of precision, speed, and reliability. First, the automated guided vehicle AGV ConTrax® Module One from BÄR Automation delivers the cable set. Once it reaches the work station, the real Robotik Challenge begins, with both Diana 7 robots executing the process steps in parallel.
The process steps in detail
Before the application starts, the AGV positions the pre-assembled table at the robot station. Two Diana 7 robots then detect tags attached to the table surface that refer to a higher-level coordinate system. This data enables precise calibration of the table in relation to the robot positions.
First, both robots grip the cable ends in parallel and guide them through the cable fixtures. They then use the 2D camera to determine the crimp position and alignment, correct it to ensure a precise fit and thus enable the crimp to be inserted into the connector.
Meanwhile, the force/torque sensor detects the forces involved to reduce friction during insertion. The sensor also verifies the final position of the crimps. This procedure is repeated for each of the five wires. Once all the crimps have been positioned in the connectors, the secondary locks are automatically closed by a magnetic mechanism.
One robot then places the connectors into a housing, while another uses a cable tie tool to attach five cable ties to the harness.
In 2:25 minutes, the partial wire harness is completed.
The Challenges
The Robotik Challenge lives up to its name. Achieving the main goal - successfully producing a partial wire harness - requires overcoming several hurdles. Two primary challenges stood out:
1. Localizing the crimp pose
To accurately detect the crimp position in 6D (position + rotation) with the 2D camera, we apply optimized feature matching algorithms designed for this specific task. These are used to identify consistent features across different images, ensuring the object can be recognized despite changes in lighting, perspective, or movement.
To do this, we compared the images from the 2D camera with various templates using AI-supported image processing algorithms. The templates were previously created during the calibration of the entire assembly and serve as a reference for the objects to be recognized: the crimp and the connector. They refer to specific features that are used as reference points during the matching process. Thanks to the optimized template matching approach, calibration only takes a few minutes.
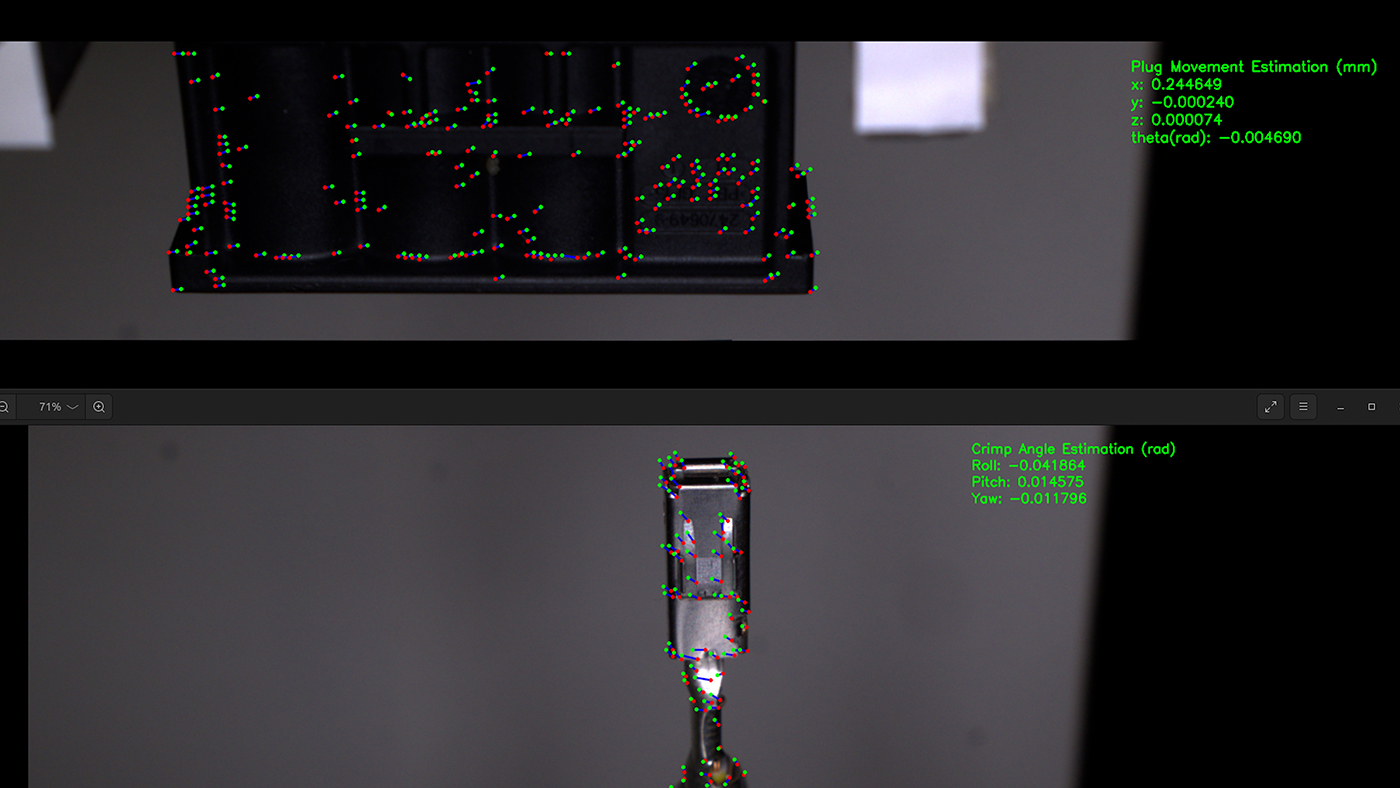
By leveraging geometric principles and defined assumptions about the system - including the crimp, wire, and gripping position - we determine the crimp's precise position and orientation relative to the connector.
Initially, the connector's properties are analyzed to establish potential variation in the alignment position. Subsequently, the crimp's characteristics are used to calculate its orientation and placement within the gripper jaws, enabling accurate alignment and insertion into the socket.
2. Handling the Nano MQS contacts
Nano MQS contacts are commonly used in wire harness assembly. These small connectors are specifically designed for electrical connections in compact applications. Their small size complicates optical detection and demands a high level of precision during installation. Consequently, we adopted a force-based search strategy that relies on a human-like sense of touch.
By touching, pressing, or moving the crimp, the robot gathers feedback about the condition of the socket, allowing it to determine the precise placement and orientation of the crimp. This process demands maximum precision - not only to insert the crimps into the housing with sub-millimeter accuracy, but also to prevent any damage during insertion.
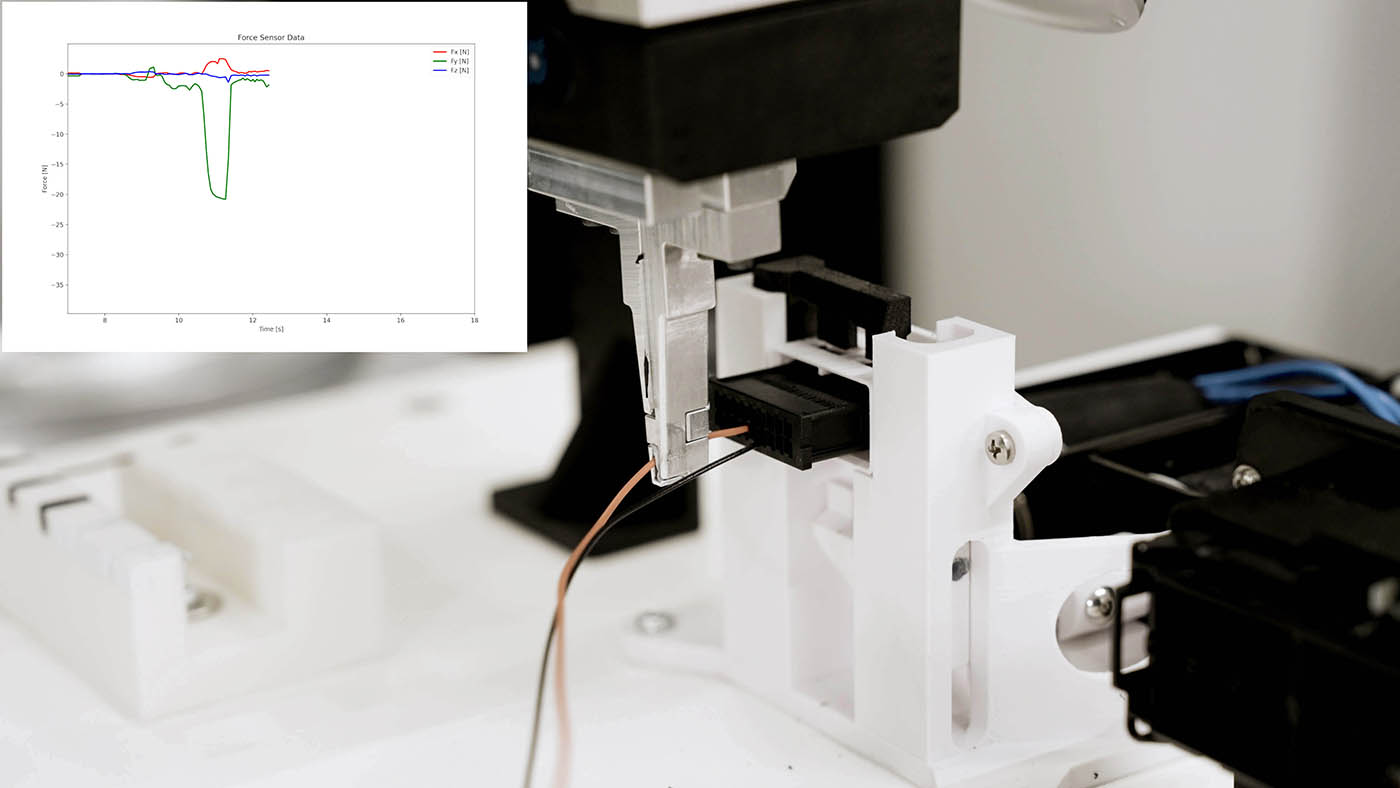
With the help of the force-torque sensor, we determined the direction of the acting forces and then corrected them accordingly. We used a control engineering method that enables the robots to respond sensitively to external forces. This concerns the Cartesian velocities, which are controlled proportionally to the measured force: if the robot senses resistance, it slows down and continues to move cautiously, as long as the resistance remains within tolerance. The tight arrangement of the cables made placement even more difficult.
Thanks to precise parameter settings and additional cable routing, the Nano MQS contacts could nevertheless be positioned reliably and accurately.
Programming with AgileCore
Our powerful software platform, AgileCore, enables the programming, control, and monitoring of the entire assembly process. It synchronizes the robots, supports direct integration of external systems, abstracts the hardware, and simplifies programming. In addition, it ensures seamless integration into existing manufacturing structures.
As part of the Robotik Challenge, specific skills were developed that can also be effectively applied to future automation solutions in the wire harness domain. These include precise table calibration and initialization, sensitive routing of individual wires, accurate installation of crimp contacts, and force-controlled placement of connectors. Thanks to AgileCore’s skill library, these capabilities can be easily parameterized, extended at will, and reproduced - making them usable for a wide range of further applications.
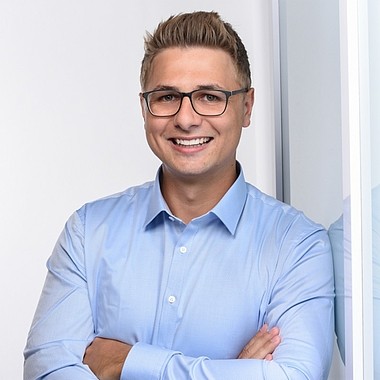
Our participation in the Robotik Challenge showed how quickly and precisely our robots can carry out even complex tasks in the field of wire harness assembly. Additionally, we gained valuable insights that will be applied to future projects. Securing first place in the Economic efficiency category is a testament to our success.
Our conclusion
The Robotik Challenge illustrates just how many different components and disciplines are required to effectively automate complex production processes.
That’s why Agile Robots follows a holistic approach - one that goes far beyond the manufacturing of robotic arms and hands. We consider the entire technology stack, from hardware to software, combined with cutting-edge artificial intelligence. The Robotik Challenge, which integrates robots, sensors, vision systems, and various peripheral devices, highlights this expertise. Agile Robots delivers tailor-made solutions, specifically adapted to meet each customer’s needs and easily customizable when required.
Our solution also emphasizes the practical use of AI: without the interplay between artificial intelligence, force sensing, and 2D cameras, the precise detection, alignment, and placement of crimps would have been significantly more difficult.
The deeper reason behind automation also becomes clear. Our disruptive application demonstrates how automation solutions can relieve both production processes and the people behind them. It boosts assembly efficiency while taking over tasks that are especially strenuous due to their monotonous and repetitive nature.
Agile Robots looks forward to applying the insights and results of the Robotik Challenge across various industries. Several leading cable harness manufacturers who witnessed the challenge live at the ARENA2036 research campus in Stuttgart have already expressed strong interest.