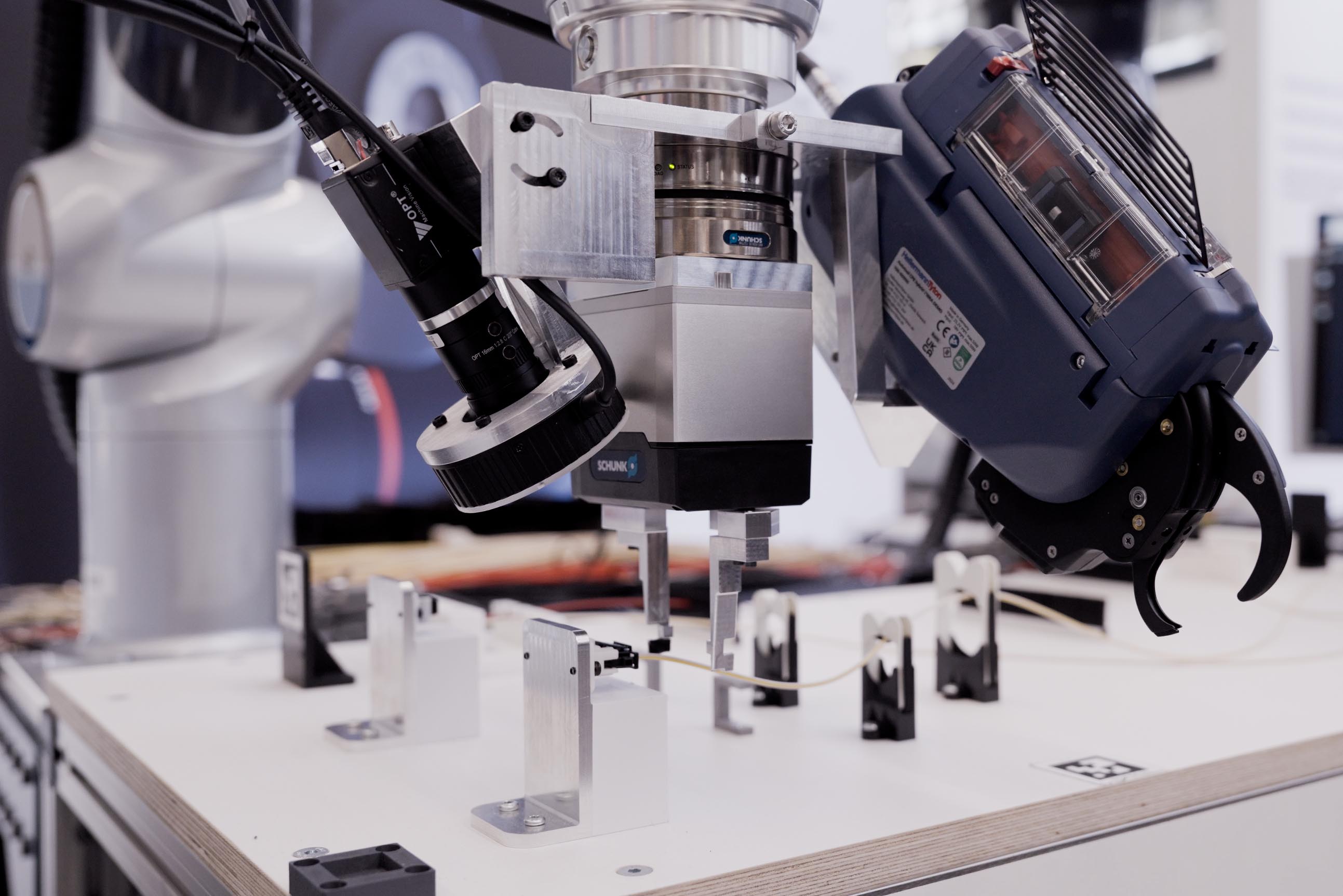
Robotik Challenge 2025: Die Lösung hinter dem Award
/ 5 Min. zu lesenDas öffentlich geförderte Projekt Transformations-Hub Leitungssatz hat auch in diesem Jahr zur Robotik Challenge am Forschungscampus ARENA2036 in Stuttgart eingeladen. Im Mittelpunkt steht die automatisierte Fertigung von Teilleitungssätzen - ein Bereich der Automobilfertigung, der bislang kaum automatisiert wurde. Als Mitglied der ARENA2036 und führender Anbieter KI-gestützter Automatisierungslösungen haben wir eine innovative Lösung entwickelt, die diese Herausforderung mit menschenähnlichem Feingefühl in nur 2:25 Minuten bewältigt – und damit 35 Sekunden unter der geforderten Taktzeit liegt. Als schnellstes Team wurden wir dafür mit dem Award für “Wirtschaftlichkeit” ausgezeichnet.
Die Aufgabenstellung
Der Leitungssatz eines Fahrzeugs, der auch als Kabelbaum bezeichnet wird, umfasst oft mehrere Kilometer Kabel und stellt das Nervensystem des Autos dar. Er besteht aus Leitungen, Steckern, Sensoren und Schutzummantelungen und sorgt für die reibungslose Signalübertragung sowie die Energieversorgung zwischen allen elektrischen und elektronischen Komponenten.
Der Teilleitungssatz, der im Zentrum der Robotik Challenge steht, ist eine Untereinheit des vollständigen Leitungssatzes: Im Rahmen der Aufgabenstellung müssen fünf Leitungen in vier verschiedenen Steckern platziert werden. Dabei kommen unter anderem Nano MQS Kontakte, Niederquerschnittsleitungen, Steckverbinder, sowie Kabelbinder zum Einsatz.
Trotz der voranschreitenden Automatisierung wird die Fertigung noch immer hauptsächlich manuell durchgeführt. Das ist auf ihre hohe Komplexität zurückzuführen: Viele Roboter scheitern an der benötigten Geschicklichkeit, der hohen Variabilität und der erforderlichen Präzision.
Die Handhabung der biegeschlaffen Kabel erfordert große Geschicklichkeit, während die Steckverbindungen exakt positioniert und die angewendete Kraft sorgfältig reguliert werden muss. Dafür sind intelligente Technologien wie fortschrittliche Sensoren und KI-gestützte Kamerasysteme notwendig.
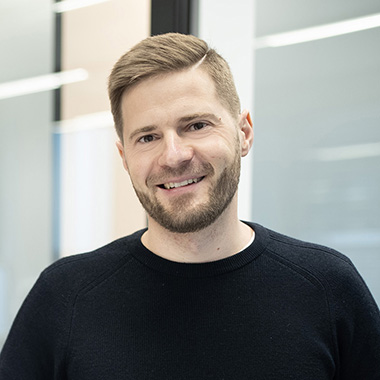
Die manuelle Fertigung des vorgegebenen Teilleitungssatzes dauert für Fachkräfte circa zwei Minuten. Unser Ziel war es, möglichst nah an diesen Wert heranzukommen, um die Effizienz der Roboterautomatisierung klar aufzuzeigen. Mit einer Taktzeit von unter zweieinhalb Minuten haben wir dieses Ziel erfolgreich erreicht – und wurden als schnellstes Team mit dem Award für Wirtschaftlichkeit belohnt.
Um die Robotik Challenge schnell, effektiv und präzise umzusetzen, setzt unser Team auf die Unterstützung von zwei Diana 7 Robotern. Die Siebenachser sind hochgradig flexibel, leistungsstark und besonders präzise. Zudem kommen u.a. zwei 2D-Kamerasysteme mit Ringlicht, sowie externe Kraft-Momenten-Sensoren, ein Kabelbinder-Werkzeug und mehrere Magnetschließer zum Einsatz.
Der Montageprozess ist in verschiedene, sorgfältig getaktete Arbeitsschritte aufgeteilt, die Präzision, Geschwindigkeit und Zuverlässigkeit miteinander vereinen. Zunächst liefert das Fahrerlose Transportfahrzeug ConTrax® Module One von BÄR Automation den Kabelsatz an. Sobald dieser den Arbeitsbereich erreicht, startet die eigentliche Robotik Challenge. Dabei führen beide Diana 7 die Prozessschritte parallel zueinander aus.
Die Prozessschritte im Detail
Vor Beginn der Anwendung positioniert das AGV den vorkonfektionierten Tisch an der Roboterstation. Anschließend erfassen zwei Diana 7 Roboter auf der Tischoberfläche angebrachte Tags, die auf ein übergeordnetes Koordinatensystem verweisen. Diese Daten ermöglichen eine präzise Kalibrierung des Tisches in Bezug auf die Roboterpositionen.
Dann greifen beide Roboter parallel die Leitungsenden und führen sie durch die Kabelfixierungen. Anschließend bestimmen sie mithilfe der 2D-Kamera die Crimp-Position und Ausrichtung, korrigieren diese passgenau und ermöglichen so das präzise Einführen des Crimps in den Stecker.
Während des Einführvorgangs misst der Kraft-Momenten-Sensor die auftretenden Kräfte, um Reibkräfte zu minimieren. Abschließend verifiziert der Sensor die Endposition der Crimps. Diese Arbeitsschritte werden dann für alle fünf Leitungen wiederholt. Sind alle Crimps in den Steckern positioniert, werden die Sekundärverriegelungen durch einen Magnetmechanismus automatisch geschlossen.
Anschließend platziert ein Roboter die Stecker in ein Umgehäuse, während der andere ein Kabelbinder-Werkzeug nutzt, um insgesamt fünf Kabelbinder am Teilleitungssatz zu befestigen.
Nach 2:25 Minuten ist der Teilleitungssatz fertig produziert.
Die Herausforderungen
Die Robotik Challenge trägt ihren Namen nicht ohne Grund. Um das Hauptziel - die erfolgreiche Fertigung eines Teilleitungssatzes - zu realisieren, müssen zahlreiche Herausforderungen gemeistert werden. Dabei standen zwei Problemstellungen besonders im Fokus:
1. Die Lokalisierung der Crimp-Pose
Zur Bestimmung der Crimp-Position in 6D (Position + Rotation) mit der 2D-Kamera setzen wir optimierte Feature-Matching-Algorithmen ein, die speziell für diese Aufgabe adaptiert wurden. Diese werden verwendet, um gleiche Merkmale in mehreren Bildern zu finden, sodass ein Objekt trotz unterschiedlicher Perspektiven, Lichtverhältnisse oder Bewegungen erkannt wird.
Dafür haben wir die Aufnahmen der 2D-Kamera mit verschiedenen Templates abgeglichen und dabei KI-gestützte Bildverarbeitungsalgorithmen verwendet. Die Templates wurden zuvor bei der Kalibrierung des gesamten Aufbaus erstellt und dienen als Referenz für die zu erkennenden Objekte, den Crimp und den Stecker. Sie verweisen auf spezifische Merkmale, die während des Abgleichs als Referenzpunkte verwendet werden. Dank optimiertem Template-Matching-Approach dauert die Kalibrierung nur wenige Minuten.
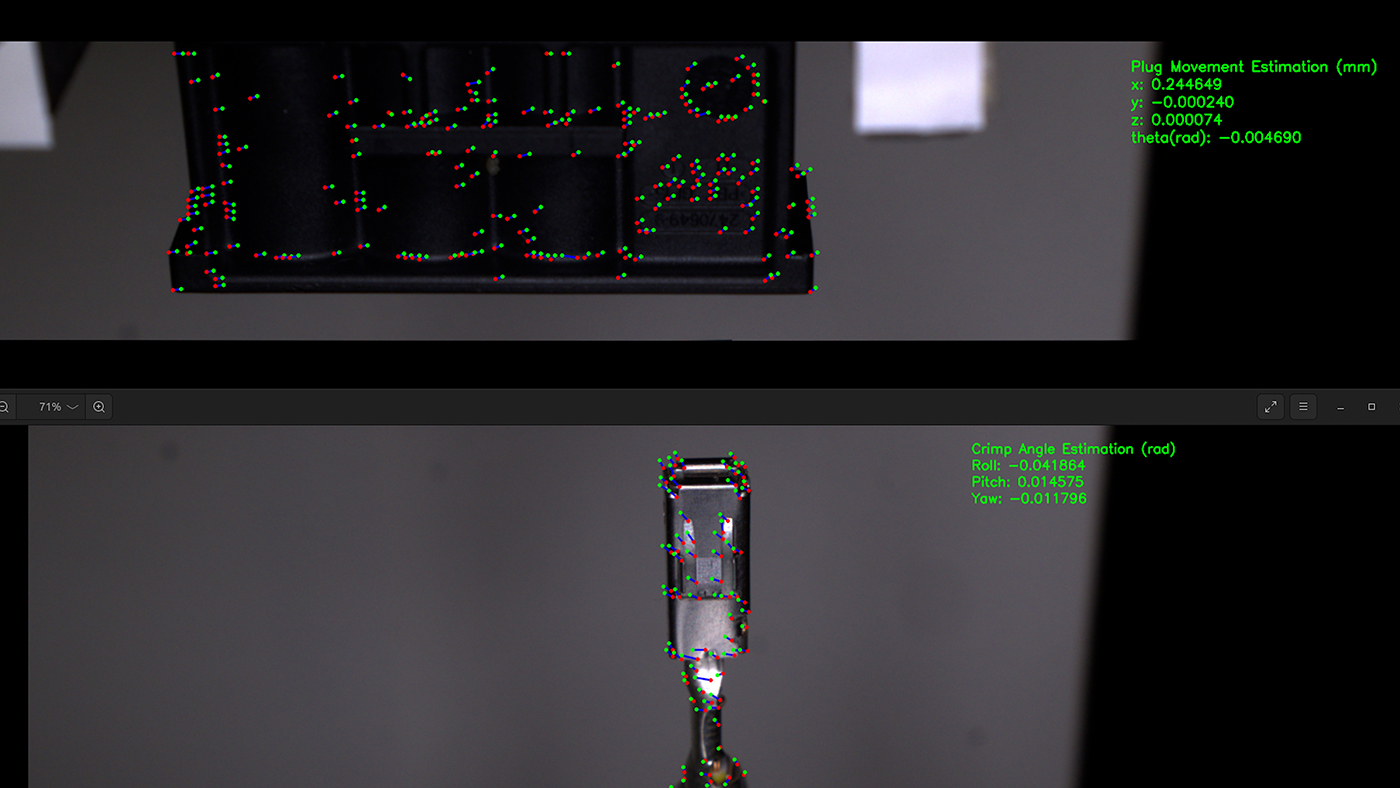
Mit Hilfe von Geometrie und spezifischen Annahmen über das System (Crimps, Leitung, Greifposition) bestimmen wir schließlich die Position und Ausrichtung des Crimps im Verhältnis zum Stecker.
Zunächst werden die Merkmale des Steckers verwendet, um eine mögliche Varianz in der Steckposition zu errechnen. Anschließend dienen die Merkmale des Crimps dazu, dessen Position und Orientierung innerhalb der Greifbacken zu bestimmen. Dadurch kann der Crimp nun präzise zur Buchse ausgerichtet und eingeführt werden.
2. Die Handhabung der Nano MQS Kontakte
In der Leitungssatzmontage werden vorwiegend Nano MQS (Miniaturisierte Qualifizierte Stecker) Crimps verwendet. Dabei handelt es sich um kleine Steckverbinder, die speziell für elektrische Verbindungen in kompakten Anwendungen entwickelt wurden. Das erschwert die optische Erkennung sowie die Installation der Crimps und setzt einen hohen Präzisionsgrad voraus. Deshalb haben wir uns für eine kraftbasierte Suchstrategie entschieden, die auf einen menschenähnlichen Tastsinn vertraut.
Durch das Tasten, Drücken oder Bewegen des Crimp erhält der Roboter Informationen über die Beschaffenheit der Buchse, die ihm signalisieren, wie und wo er den Crimp platzieren muss. Dabei ist höchste Präzision gefragt. Zum einen, um die Crimps sub-millimetergenau im Gehäuse einzusetzen, zum anderen, um diese während des Einsteckens nicht zu beschädigen.
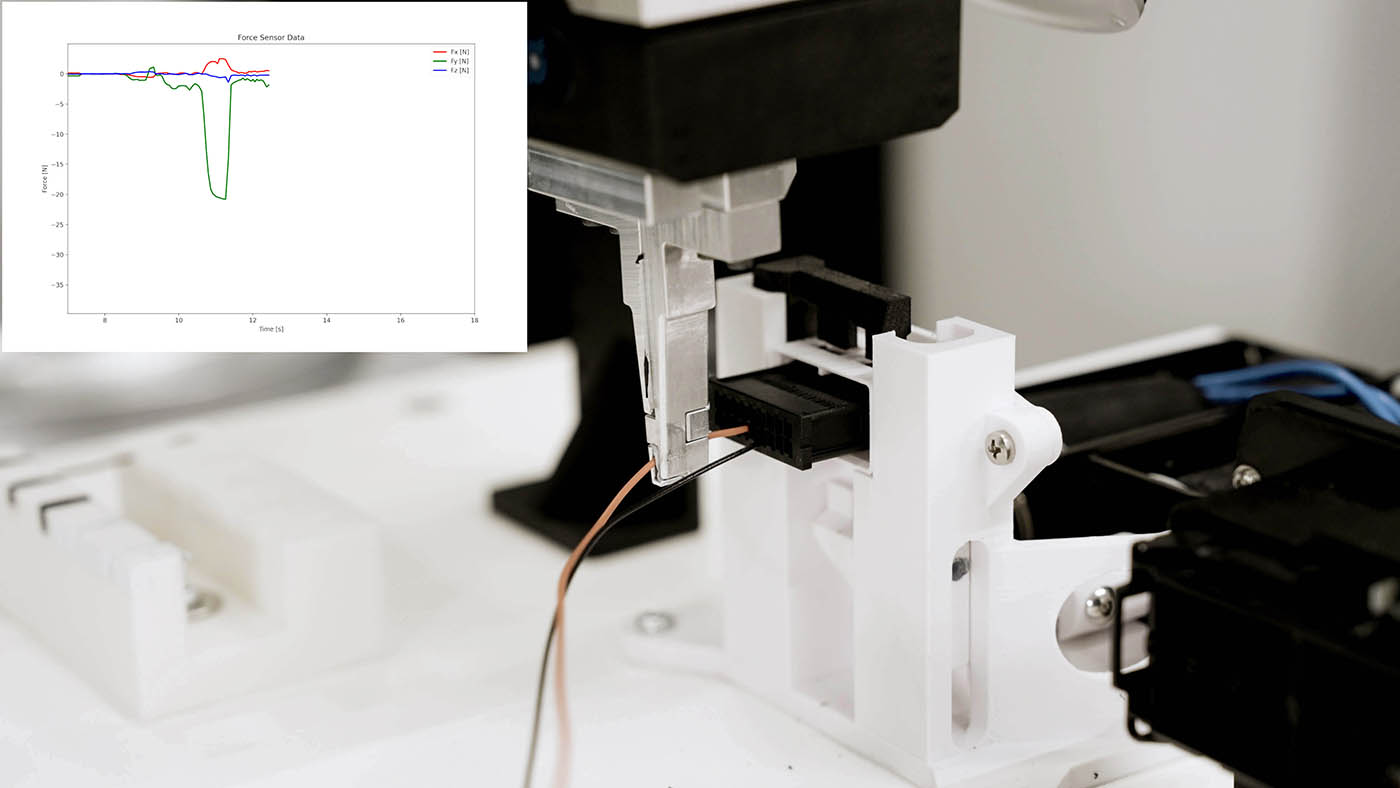
Mithilfe des Kraft-Momenten-Sensors haben wir die Richtung der wirkenden Kräfte bestimmt und sie dann entsprechend korrigiert. Dabei setzen wir auf eine regelungstechnische Methode, die es den Robotern ermöglicht, sensibel auf externe Kräfte zu reagieren. Das betrifft die kartesischen Geschwindigkeiten, die proportional zur gemessenen Kraft gesteuert werden: Spürt der Roboter einen Widerstand, verlangsamt er und bewegt sich vorsichtig weiter, sofern der Widerstand innerhalb der Toleranz bleibt. Die enge Anordnung der Kabel erschwerte die Platzierung zusätzlich.
Dank präziser Parametereinstellungen und zusätzlicher Leitungsführungen konnten die Nano MQS Kontakte dennoch zuverlässig und genau eingesetzt werden.
Programmierung durch AgileCore
Unsere leistungsstarke Softwareplattform AgileCore ermöglicht die Programmierung, Steuerung und Überwachung des gesamten Montageprozesses. Sie synchronisiert die Roboter, unterstützt die direkte Anbindung externer Systeme, abstrahiert die Hardware, und erleichtert die Programmierung. Zudem gewährleistet sie eine reibungslose Integration in bestehende Fertigungsstrukturen.
Im Rahmen der Robotik Challenge wurden spezifische Skills entwickelt, die auch für künftige Automatisierungslösungen im Leitungssatzbereich effektiv eingesetzt werden können. Dazu zählen unter anderem die präzise Tischeinmessung und Initialisierung, die sensitive Verlegung von Einzelleitungen, die exakte Installation von Crimp-Kontakten sowie das kraftgeregelte Platzieren von Steckern. Dank der Skill-Bibliothek von AgileCore können diese Fähigkeiten einfach parametrisiert, beliebig erweitert und reproduziert werden. Somit sind sie für eine Vielzahl weiterer Anwendungen nutzbar.
Durch den holistischen Ansatz der Software verfügt der Nutzer über alle Instrumente, die er für den Automatisierungsprozess benötigt – zentralisiert auf nur einer Plattform.
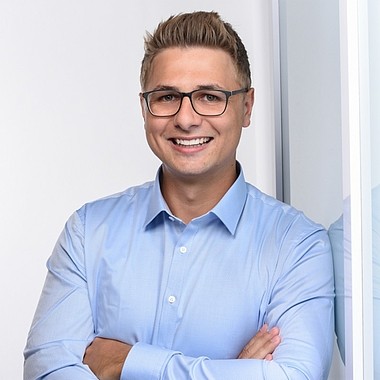
Unsere Teilnahme an der Robotik Challenge hat gezeigt, wie schnell und präzise unsere Roboter auch komplexe Aufgaben im Bereich der Leitungssatzmontage realisieren können. Außerdem haben wir uns viele neue Kenntnisse angeeignet, die wir auch künftig für ähnliche Projekte nutzen können. Der erste Platz im Bereich Wirtschaftlichkeit bestätigt das.
Unser Fazit
Die Robotik Challenge veranschaulicht, wie viele verschiedene Komponenten und Disziplinen erforderlich sind, um komplexe Produktionsprozesse effektiv zu automatisieren.
Deshalb setzt Agile Robots auf einen holistischen Ansatz, der über die Fertigung von Roboterarmen und Händen hinausgeht und den gesamten Technologie-Stack berücksichtigt – von der Hardware bis zur Software, in Kombination mit modernster künstlicher Intelligenz. Die Robotik Challenge, die Roboter, Sensoren, Vision-Systeme und verschiedene Peripheriegeräte kombiniert, unterstreicht diese Kompetenz. Agile Robots bietet maßgeschneiderte Lösungen, die speziell auf die Bedürfnisse des Kunden zugeschnitten und bei Bedarf adaptiert werden können.
Zudem betont unsere Lösung den praktischen Einsatz von KI: Ohne das Zusammenspiel zwischen künstlicher Intelligenz, Kraftsensorik und 2D-Kameras wäre die präzise Erkennung, Ausrichtung und Platzierung der Crimps nur schwer realisierbar.
Auch der übergeordnete Grund hinter der Automatisierung wird deutlich. Unsere disruptive Anwendung zeigt auf, wie Automatisierungslösungen sowohl die Produktionsprozesse als auch die Mitarbeiter dahinter entlasten können. Sie steigert die Effizienz der Montage und übernimmt dabei Tätigkeiten, die aufgrund ihrer monotonen und repetitiven Arbeitsweise besonders belastend sind.
Agile Robots freut sich darauf, die gewonnenen Erkenntnisse und Ergebnisse aus der Robotik Challenge in verschiedenen Branchen umzusetzen. Mehrere führende Kabelkonfektionäre, die die Challenge live im Forschungscampus ARENA2036 in Stuttgart verfolgten, bekundeten bereits ihr Interesse.